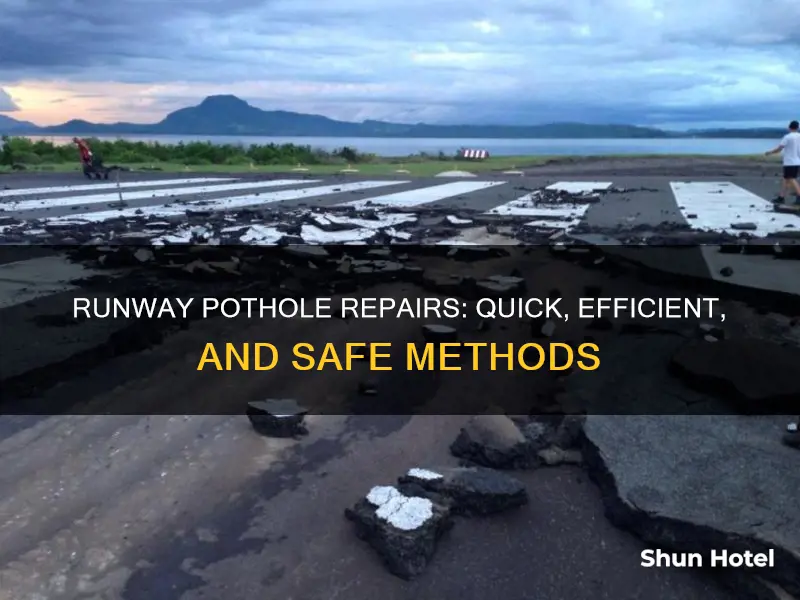
Airport runways are subjected to a lot of wear and tear, from the weight of huge planes landing and taking off to extreme weather conditions. This can lead to cracks and potholes, which can be dangerous for aircraft, causing loss of control or damage to engines. Airports take several preventative measures to avoid this, including regular inspections and sealing cracks with hot pour crack filler or asphalt sealer. Despite these measures, sometimes repairs are necessary, and runways must be closed for short periods to carry out maintenance.
Characteristics and Values of Airport Runway Pothole Repairs
Characteristics | Values |
---|---|
Runway Maintenance Frequency | Annually or biannually |
Runway Maintenance Time | Night, between 11 PM and 5 AM |
Maintenance Duration | A few hours to a full day or more |
Maintenance Tasks | Joint sealing, crack repairing, patching potholes, sealing open cracks and joints, removing skid marks, sweeping, cutting grass |
Materials Used | Asphalt, concrete, reinforced concrete, composite pavements, subbase materials, grooved surfaces, geotextiles, chemical solvents, high-pressure water, hot compressed air |
Preventative Measures | Regular inspections, seal coating, asphalt sealers, hot pour crack filler |
What You'll Learn
Maintenance schedules to prevent potholes
Maintenance schedules are crucial to preventing potholes on airport runways. Regular maintenance can seal cracks that can enlarge and become potholes, reducing the need for more extensive runway repairs. Here are some key aspects of maintenance schedules aimed at preventing potholes:
Regular Inspections and Maintenance
Runways should be inspected daily for any visible cracks or signs of deterioration. This proactive approach enables maintenance crews to identify issues early on and make necessary repairs before they escalate into potholes.
Crack Sealing and Repair
Crack sealing is a vital aspect of runway maintenance. Small cracks can quickly turn into potholes due to the constant stress of aircraft landings and take-offs. Using a hot pour rubberized crack filler is recommended for runway repairs as it dries quickly (within about two hours) and increases the runway's durability. This rapid repair method minimizes the inconvenience of prolonged runway closures.
Preventative Maintenance
In addition to crack sealing, preventative measures such as asphalt sealers can protect the runway surface from environmental factors like sun, rain, snow, and ice. Sealcoating repels water, preventing it from infiltrating small cracks and causing further damage. This maintenance technique is especially beneficial in regions with extreme temperature fluctuations, which can cause significant asphalt expansion and contraction, leading to cracking.
Routine Maintenance Operations
Major airports aim to conduct as many short maintenance operations as possible during off-peak hours, typically at night. This strategy minimizes disruptions to air traffic while allowing for regular runway upkeep. Some maintenance tasks may require closing the runway for a day or more if they cannot be completed within a single night.
Weather-Related Maintenance
Airports in regions with distinct weather patterns, such as monsoons or freezing temperatures, should schedule maintenance to address weather-related wear and tear. For example, Mumbai's Chhatrapati Shivaji Maharaj International Airport schedules yearly maintenance and additional pre-and post-monsoon prep to protect its runways from rain-related damage.
By implementing these comprehensive maintenance schedules, airports can effectively prevent potholes and maintain the safety and functionality of their runways.
Denver Airport: Are There Private Sleeping Rooms Available?
You may want to see also
Repairing methods
Runway repairs are a challenge for airports due to the potential disruption to flight operations. Potholes on runways can cause serious damage to aircraft engines and result in loss of control during landing. Therefore, airports put in a lot of effort to prevent and repair such damage, and routinely inspect their runways.
To prevent excessive runway repairs, it is necessary to establish a regular maintenance schedule to seal cracks that can quickly enlarge and become potholes. The best way to accomplish this type of airport runway repair is to proactively use a hot pour crack filler to substantially reduce accelerated runway deterioration. Hot pour rubberized crack filler is recommended for use on runways as it dries quickly (in about two hours) and increases runway durability.
Asphalt sealers are also used to protect asphalt against sun, rain, snow, and ice. This type of sealer repels water from the surface, preventing water from penetrating small cracks that can lead to greater damage. It is also resistant to oil, gasoline, salt, and other staining agents.
Some airports schedule yearly maintenance of their runways to protect them from rain-related wear and tear. For example, Mumbai's Chhatrapati Shivaji Maharaj International Airport (BOM) in India schedules yearly maintenance and preps its runways twice a year, both pre- and post-monsoon.
For major airports like JFK or O'Hare, the challenge is to conduct repairs with little to no impact on traffic. Resurfacing an entire runway can take a long time, so airports try to do as many short maintenance operations as possible at night. Some airports divide the runway into sub-sections and evaluate a different section every month or every other month, ensuring that each section is inspected twice a year.
Gowanda, NY: Airport Accessibility and Travel Options
You may want to see also
Impact on airport operations
The impact of pothole repairs on airport operations can vary depending on the size of the airport, the number of runways, and the extent of the damage. In some cases, such as at smaller airports with limited resources, pothole repairs may require the complete closure of the runway for a few hours, resulting in flight delays and cancellations. Larger airports, on the other hand, may have more flexibility in conducting repairs during off-peak hours or by utilizing multiple runways to minimize disruptions to flight operations.
To reduce the impact on airport operations, preventative maintenance is crucial. Regular inspections, crack sealing, and joint resealing are performed to prevent the formation of potholes and more extensive damage. Some airports also schedule yearly maintenance to protect runways from weather-related wear and tear, such as rain or extreme temperature fluctuations, which can cause significant contraction and expansion of the asphalt, leading to cracking.
When potholes or other types of damage are detected, airports must assess the severity and determine the appropriate course of action. Minor repairs can often be completed quickly, with minimal impact on flight operations. For example, the use of rapid runway repair techniques, such as hot pour crack fillers, can substantially reduce the time needed for repairs, preventing prolonged disruptions.
However, in cases of more extensive damage, longer closures may be unavoidable. This can involve dividing the repair work into several perfectly timed tasks, typically performed during the night when flight traffic is lower. For instance, the French airport Orly (ORY) replaces one slab of concrete on its runway every night, allowing the strip to be renewed without disturbing traffic.
The impact of pothole repairs on airport operations also depends on the materials used for the runway. Asphalt runways are generally easier and quicker to repair than concrete runways. The flexibility of asphalt allows it to accommodate slight ground movements without cracking, reducing the need for frequent repairs. Additionally, asphalt sealers can be applied to protect the surface from environmental factors, further minimizing the need for rapid runway repairs.
Airport Temperature Checks: Effective or Security Theater?
You may want to see also
Runway inspection
Runway maintenance and repair are crucial to airport operations, ensuring the safety of aircraft and maintaining efficient flight operations. Regular runway inspections are conducted to identify and address various issues, including potholes, cracks, and foreign objects on the runway surface. Here is a detailed overview of the runway inspection process:
- Visual Inspection: A visual inspection of the runway is performed daily to identify any visible cracks, potholes, or other surface damages. This involves a thorough examination of the runway surface to detect any potential issues that may compromise the safety of aircraft operations.
- Structural Condition Assessment: Specialized trucks equipped with advanced sensors are used to evaluate the structural integrity of the runway. These sensors capture data about the runway's condition as the trucks drive up and down the runway. This data is then analyzed to create a detailed map of the runway's condition, helping to identify areas that require maintenance or repair.
- Foreign Object Detection: Airports use airport fire trucks or other vehicles to inspect the runway for foreign objects multiple times a day. This is a critical safety measure to prevent debris, such as loose equipment or parts, from posing a hazard to aircraft during take-off and landing.
- Sub-Section Evaluation: To ensure comprehensive coverage, the runway may be divided into sub-sections, with each section evaluated periodically, typically every month or every other month. This approach enables a more focused and detailed inspection, ensuring that no area is overlooked.
- Sweeping and Maintenance: In addition to inspections, regular sweeping is performed to prevent the accumulation of grass, dirt, pebbles, and other debris. This maintenance activity helps maintain a clear and safe runway surface, reducing the risk of foreign object debris (FOD) damage to aircraft.
- Joint and Crack Maintenance: Repairing and resealing cracks and joints in the runway pavement is crucial to preventing water infiltration, which can lead to more significant issues, including pothole formation. Airports use various materials, such as hot pour rubberized crack fillers, to seal these cracks and increase the runway's durability.
- Comparison with Previous Inspections: To assess the effectiveness of maintenance and repair work, the results of each runway inspection are compared with those of the previous inspection. This allows for a continuous improvement process, helping to identify recurring issues and optimize maintenance strategies.
Tragic Human Loss at Kabul Airport: Counting the Dead
You may want to see also
Materials used
The materials used to repair airport runway potholes must be able to withstand heavy aircraft loads, frequent usage, and weather extremes. The most common materials used in runway construction and repair are asphalt, concrete, reinforced concrete, and composite pavements.
Asphalt is a flexible composite material made of aggregates such as sand, gravel, and crushed stone bound together with bitumen, a sticky, black, and highly viscous liquid or semi-solid form of petroleum. Its flexibility allows it to accommodate slight ground movements without cracking, making it suitable for areas with variable temperatures and ground conditions. Asphalt also provides a smooth surface that reduces wear and tear on aircraft tires and landing gear. In addition, asphalt is easier and quicker to repair compared to concrete. Potholes and surface damages can be patched quickly, minimizing runway downtime. To prevent excessive runway repairs, it is recommended to use a hot pour crack filler, such as a hot pour rubberized crack filler, to seal cracks and increase runway durability.
Concrete is another material used in runway construction and repair. It offers enhanced strength and resistance to damage compared to non-reinforced concrete. Reinforced concrete incorporates steel bars (rebar) or mesh within the concrete to increase its tensile strength and load-bearing capacity. This makes it capable of withstanding greater tensile stresses and heavy aircraft loads. Reinforced concrete also has a long lifespan and requires minimal maintenance. However, concrete is prone to cracking, especially in freeze-thaw conditions, and repairing concrete cracks can be more challenging and costly than asphalt repairs. Concrete also requires a significant curing period before it can be used, which can delay the runway's availability.
Composite pavements are another option for runway repair, offering a combination of materials to enhance the runway's performance, durability, and safety. Specialized subbase materials, grooved surfaces, and geotextiles are used to improve braking performance and overall runway usability during wet conditions.
Dallas Airport: A Sprawling Transportation Hub
You may want to see also
Frequently asked questions
Airport runways need repairs due to the stresses imposed on the asphalt by take-offs, landings, extended wait times, and taxiing. In addition, extreme temperature fluctuations can cause significant contraction and expansion of the asphalt, leading to cracking.
The maintenance cycle differs depending on the airport and the type of runway surface. Some airports have an annual "major maintenance" day, while others schedule yearly maintenance with additional prep before and after the monsoon season.
Airport runway potholes are repaired by patching the potholes and sealing cracks with a hot pour crack filler. This prevents water from infiltrating under the runway and causing further damage.
The time required to repair an airport runway depends on the extent of the repairs. Some repairs can be done in a single night, while others may require the airport to close for a day or more.
Airports try to minimise the impact of runway repairs on flight operations by conducting as many short maintenance operations as possible at night. For larger projects, some airports may shorten the runway to allow smaller jets to continue operating, while larger planes are redirected to a different runway.