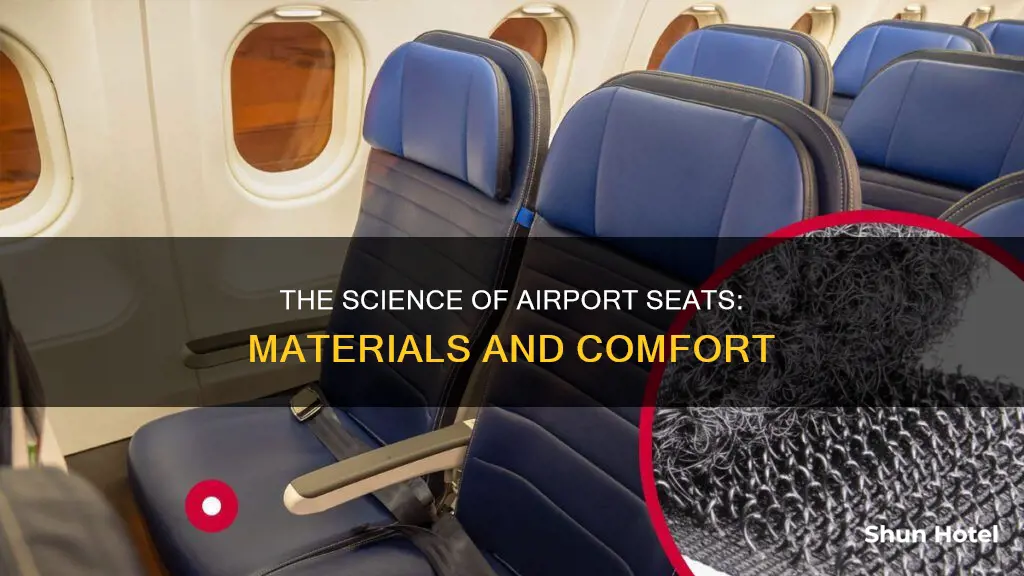
Airport seating has evolved to meet the needs of modern travellers, with a focus on comfort, functionality, and aesthetics. Airports have increased seating in lobbies and waiting areas to accommodate passengers' extended wait times due to heightened security measures. Airport planners and designers collaborate to create innovative solutions that enhance the overall traveller experience. This includes providing various seating options, such as clusters, benches, and modular configurations, to cater to different preferences and needs. Additionally, the introduction of sleeping pods in some airports offers travellers a private and peaceful space to relax or work while waiting for their flights.
What You'll Learn
Materials used for airport seats
Airport seating has evolved over the years, with designers prioritising the traveller experience by providing comfortable seating in terminals. The materials used for airport seats vary, with different sections having their own unique requirements.
The primary components of an aircraft seat are structure, upholstery, cushioning, and plastic moulding. Traditionally, the structural frame member, which provides weight support and shape to the seat, was made of steel or aluminium. However, advancements in technology have led to the use of carbon-fibre composites, which offer the advantage of being incredibly lightweight.
The seat base is often made of a shallow steel trough, while some newer designs use aluminium with a backrest structure made of rolled high-tensile steel for better energy absorption in the event of a crash. Composite structures, which include cushions, springs, and upholstery, are also considered for their comfort and load distribution capabilities.
Cushion filling is typically made from synthetic materials like polyurethane, neoprene, silicone, and polyethylene. Fire-blocking textiles are also included for safety. Upholstery can vary between synthetic and natural materials, with premium cabins often featuring natural materials such as leather and cotton.
Plastic moulding is used for tray tables, armrests, and areas surrounding entertainment screens. It is made from materials such as polycarbonate, vinyl, and heat-resistant or flame-retardant thermoplastics to meet fire safety regulations.
Overall, the materials chosen for airport seating must consider safety, comfort, and functionality, while also taking into account weight and energy-saving factors.
Midway Airport: Chicago's Busy Travel Hub
You may want to see also
Design and comfort considerations
Airport seating has to take into account a variety of design and comfort considerations. The design of airport seating can be influenced by factors such as the airport's brand identity, the available space, expected passenger traffic, and the level of comfort required. The space surrounding the seating area within an airport is designed to encourage comfort, happiness, and connectedness among travellers.
The level of comfort travellers experience is dependent on a variety of factors, including the scent of the waiting area, the distance between seats, and the amount of legroom. The arrangement of chairs in rigid lines bolted to the floor discourages social interaction, while the presence of armrests increases the usage of chairs and helps strangers feel more comfortable sitting adjacent to each other. The parallel orientation of modular seat units also minimises face-to-face contact, making it seem less threatening for strangers.
The design of airport seating must also consider factors such as ergonomics, accessibility, and the overall user experience to create seating that is both functional and aesthetically pleasing. The cost of materials and production can also affect design choices. For example, to save fuel costs, lightweight designs are preferred for aircraft interiors. Composite structures, which provide optimum contact and comfort through contour and seating geometry, are highly considered for seat design.
The comfort of airport seating has become increasingly important due to the rise in wait times caused by increased airport security measures. Airports have made efforts to increase seating in lobbies and seating areas to accommodate customer experience. Some airports provide more comfortable and spacious seating in membership-based lounges, while others have introduced sleeping pods, allowing travellers to relax in their own peaceful space.
The Science Behind Airports' X-ray Vision for Bags
You may want to see also
Safety and fire regulations
In the context of fire safety, airport seats and aircraft seats are subject to different regulatory frameworks. Airport seats, as part of the airport terminal infrastructure, are governed by regulations specific to the country or region. These regulations dictate the materials used for the seats to ensure they meet fire safety standards. The specific fire safety standards for airport seats may include requirements for flame-retardant materials, smoke emission limits, and ignition resistance properties. The regulations aim to mitigate the risk of fire spread and ensure the safety of passengers and staff in the event of a fire.
On the other hand, aircraft seats are subject to aviation safety standards, which include fire safety regulations. Aircraft seats must be made of fire-resistant materials, and this consideration applies to all parts of the seat, including the structure, upholstery, cushioning, and plastic molding. The Federal Aviation Administration (FAA) in the United States, for example, has established stringent standards for aircraft seat safety, including fire performance requirements.
Aircraft seat materials are carefully selected to meet these fire safety standards. The cushion filling, for instance, often incorporates fire-blocking textiles alongside synthetic materials like polyurethane, neoprene, silicone, and polyethylene. The upholstery, which can be made from synthetic or organic materials, is also chosen with fire safety in mind. Natural materials like leather and cotton might be more common in premium cabins, while synthetic options such as polyester and nylon are used as well.
Additionally, the design of aircraft seats considers the overall safety of passengers, including children. The FAA recommends the use of approved Child Restraint Systems (CRS) or Child Aviation Restraint Systems (CARES) for children's safety. These devices provide additional protection for children during the flight and are designed to meet aviation-safety standards. The placement of these restraint systems is also important, as they should not block the escape path in an emergency.
Sleeping Pods at LAS Airport: A Comfortable Nap?
You may want to see also
Manufacturing process
The manufacturing process for aircraft seats is complex and involves several stages. Firstly, the seat design is created using computer-aided design (CAD) software, allowing engineers to generate 3D models and assess performance in various scenarios. Subsequently, materials are selected, focusing on lightweight options like carbon fibre composites, aluminium, and high-strength alloys, which are crucial for weight reduction without compromising strength.
The next stage involves cutting and shaping the chosen materials using advanced techniques such as laser cutting, water jet cutting, or CNC machining. This stage requires skilled workers, which has been a challenge for seat manufacturers post-pandemic. The assembly process follows, with economy seats being relatively straightforward to assemble, while premium-cabin seats, such as business-class pods, are significantly more intricate due to additional features like door installation and complex wiring for entertainment systems.
Once assembled, the seats undergo rigorous testing and certification to ensure compliance with safety and performance standards, including impact resistance, fire resistance, and durability. After passing these tests, the seats are shipped to the aircraft manufacturer or airline for installation. This typically involves a team of technicians who secure the seats in the aircraft and verify their functionality.
The entire process, from design to installation, requires careful consideration of various factors, including passenger comfort, safety, durability, and weight reduction, all while meeting strict industry standards. The manufacturing process for aircraft seats has evolved over the years, allowing for the assembly of even the most luxurious seats in just a few hours.
Chicago Airport: COVID Testing Availability and Facilities
You may want to see also
Industry standards and trends
The design of airport seating has not changed significantly in over 50 years and is known for its simplicity. The primary focus of today's airport seating is the size and comfort of the seating to fit the environment that the airport and airline desire to create. Since fire safety is a significant consideration at airports, regulations now govern the contents of airport terminals, affecting the materials used for seating.
The global aircraft seating market size is projected to grow from $6.93–7.61 billion in 2024 to $11.83 billion by 2032, at a CAGR of 5.67%. The market is propelled by a dynamic landscape defined by innovation, regulatory imperatives, and industry collaborations.
Seat materials, such as seat covers and foams, are made of various materials, including nylon, synthetic leathers, silicon, polyethylene, and fireproof fabric. These materials play an important role in improving the quality of aircraft seats and life expectancy. The selection of fibre type for transportation seat fabrics has evolved over the years with the progress in fibre development and discoveries. Initially, seats were made from natural fibres such as wool and cotton, which suffer from low abrasion resistance and high moisture absorbency. Today, advanced composites and high-strength alloys are increasingly being used to enhance fuel efficiency and reduce overall aircraft weight, aligning with broader industry goals of sustainability.
Seat cover fabric can also be coated to improve performance characteristics or maintain the integrity of the fabric structure. For example, some woven fabrics may be coated with acrylic or polyurethane resin to improve flame resistance and abrasion resistance.
As aviation technology advances, the demand for cutting-edge seating solutions rises. The market's unique drivers include the continuous evolution of global durable and fire-resistant materials, the imperative for compliance with stringent safety standards, and the integration of advanced sensors and components. As airlines expand their fleets and modernise existing aircraft, the OEM segment is expected to maintain a dominant market share, reflecting the ongoing trend towards enhanced passenger comfort and operational efficiency.
The trend of replacing traditional foam material with pneumatic seat systems has been mainly based on meeting comfort and lightweight specifications. The rise in aircraft deliveries of new commercial passenger aircraft has positively driven the growth of the market. In 2021, Airbus and Boeing delivered around 950 new commercial and transport aircraft and received bulk orders from major airline operators.
Who Owns Airports? Private or Federal Control?
You may want to see also
Frequently asked questions
Airport seats are made from a variety of materials. The primary components are structure, upholstery, cushioning, and plastic molding. The structure is often made from steel or aluminum, while the upholstery can vary between synthetic and organic materials, such as polyester, nylon, leather, and cotton. The cushioning typically includes foam rubber and synthetic materials like polyurethane, neoprene, silicone, and polyethylene. Plastic molding is used for tray tables, armrests, and entertainment screens, made from materials such as polycarbonate, vinyl, and plastazote.
Airport seats are designed with comfort, durability, and safety in mind. The arrangement of seats aims to maximize the use of space while providing a sense of personal space for travelers. Fire safety is a significant consideration, influencing the materials used for seating to meet regulations. Additionally, the level of comfort offered by airport seats can vary, with membership-based lounges providing more comfortable and spacious seating options.
Yes, airport seats can vary depending on the airport and the specific area within the terminal. For example, some airports offer sleeping pods or lounge areas with more comfortable seating options, such as cushioned chairs or cluster seating configurations. These areas may require a membership or additional fees.
Airport seats and airplane seats serve different purposes and have distinct design considerations. Airport seats are typically found in public seating areas or lounges within the airport, focusing on comfort and functionality. On the other hand, airplane seats are designed for passenger accommodation during the flight, prioritizing safety and comfort within the space constraints of the aircraft. Airplane seats may have features like reclining mechanisms, adjustable lumbar support, or massaging functions, depending on the class of travel.