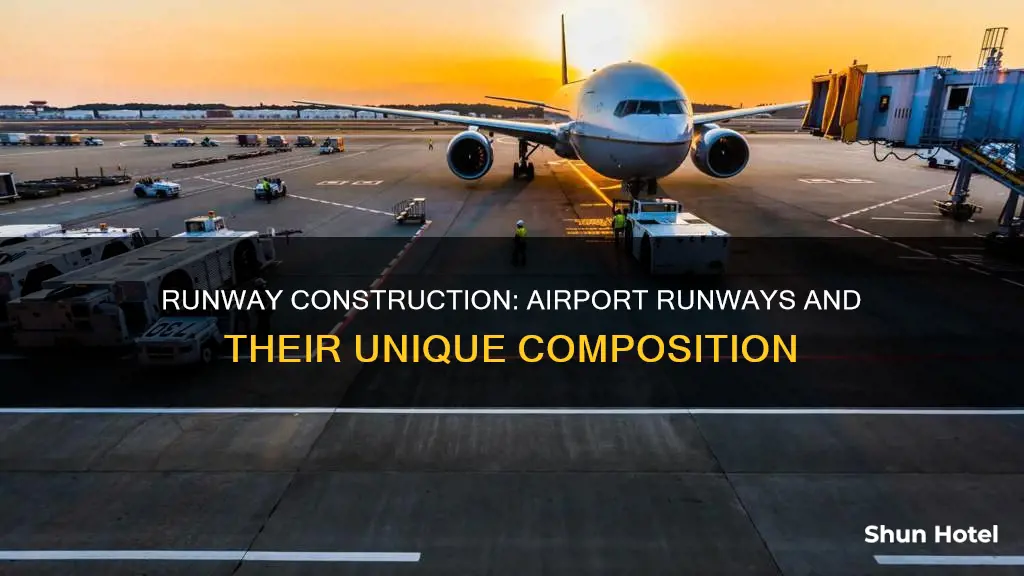
Airport runways are critical areas that handle hundreds of thousands of takeoffs and landings per year, with aircraft weighing hundreds of tons moving on and off the pavement daily. These pavements need to be firm, stable, and durable through all weather conditions to support the heavy loads imposed by airplanes. The choice of pavement material depends on local ground conditions, the type of aircraft using the facility, and cost. So, what are airport runways made of?
What You'll Learn
Asphalt vs. concrete
Airport runways must be made of exceptionally strong materials to withstand the pressure of aircraft takeoffs and landings, as well as frequent use. While runways were often made of grass and were relatively short before the heavier planes of the late 1930s, today's runways are much longer and are usually made of asphalt or concrete.
Asphalt is a liquid or semi-solid type of petroleum made from aggregate materials held together with a binder. It has a dark grey to black finish, leading to the nickname "blacktop". Asphalt is flexible and porous, which makes it more gentle on the tires during touchdown and allows it to drain well in the rain. It is also quicker and cheaper to install than concrete. However, it is more susceptible to fuel degradation, as the fuel can dissolve the asphalt holding the aggregate together. Asphalt is also more prone to deforming on warm days and cracking prematurely.
Concrete, on the other hand, is a rigid surface that handles stationary loads well. It is typically more expensive and time-consuming to install upfront, but it is often more economical over time, provided it receives the required ongoing maintenance. Concrete is also more prone to cracking when exposed to extreme temperatures. However, it is more environmentally friendly than asphalt due to asphalt's petroleum-based binder.
The choice between asphalt and concrete for runway construction depends on various factors, including climate, traffic, budget, and raw material access. Many runways feature a combination of both materials, with asphalt layered on top of concrete or vice versa. For example, New York JFK has three concrete runways and one asphalt runway.
Airport Marine's Yamaha Motor Sales: What You Need to Know
You may want to see also
Natural vs. man-made surfaces
Airport runways are designed to be firm, stable, and durable surfaces that can withstand hundreds of tons of aircraft weight through all weather conditions. The choice of surface material depends on several factors, including local ground conditions, the type of aircraft using the facility, and cost.
Natural Surfaces
Natural surfaces like grass, dirt, gravel, ice, sand, or salt are typically found at smaller airports that cater to light aircraft models or those specifically designed for such surfaces. These surfaces are generally less costly to maintain and can be more flexible in terms of location, as they don't require the same level of construction as man-made surfaces. However, they may not be suitable for larger or heavier aircraft and may be more susceptible to weather conditions.
Man-made Surfaces
Man-made surfaces, such as asphalt and concrete, are the most common choices for major commercial airports. Asphalt, a flexible surface made from aggregate materials held together with a binder, is widely used due to its relatively lower cost and quick installation. It is also more gentle on aircraft tires during landing. However, it is susceptible to fuel degradation and can deform in warm temperatures. Concrete, on the other hand, is a rigid surface that is more expensive to install and repair but is highly durable and has a longer lifespan. It is better suited for stationary aircraft and can handle the weight of larger planes.
The decision between asphalt and concrete often depends on the specific requirements of the airport, the local climate, and budgetary considerations. Some runways even feature a combination of both surfaces to cater to different needs.
Traveler's Guide: Finding ATMs at Tirana's Nënë Tereza Airport
You may want to see also
Runway maintenance
To preserve the surface integrity of the runway while removing contaminants, various methods can be employed, including high-pressure water blasting, chemical treatments, and mechanical methods like milling. Milling is a process where milling rollers comprising metal discs on a rotating channel are passed over the surface, with the distance between the shaft and the pavement controlled so that the discs just touch the pavement without much pressure. This method removes the rubber layer and roughens the pavement surface, with sweepers usually following to clean the runway of dust and rubber debris.
Proper planning and scheduling of maintenance work are crucial to minimizing disruptions to aircraft operations. Work should be scheduled during off-peak hours, and alternative runways should be available if needed. Notices to Airmen (NOTAMs) should also be issued to inform pilots of any maintenance or repair work that may affect aircraft operations.
Exploring Destin Airport: Efficient Gateways for Efficient Travel
You may want to see also
Runway construction
Asphalt, a flexible surface made from aggregate materials held together with a binder, is a common choice for runway construction. It is often used in locations with suitable climatic conditions as it can be susceptible to fuel degradation and deformation on warm days. Asphalt runways typically have a dark grey to black finish and are generally more cost-effective than concrete. The Marshall mixture, developed in 1939, is a popular composition for runway asphalt, consisting of bitumen and aggregate. Newer blends focus on making asphalt more eco-friendly and fuel-resistant, with some offering twice the lifespan of conventional asphalt.
Concrete, on the other hand, is a rigid surface that is typically more expensive to install and repair than asphalt. Concrete runways are constructed by placing Portland cement slabs on a granular subgrade or a prepared sub-base made of fine material. Concrete is known for its durability and longer lifespan, making it a common choice for major commercial airports. Concrete can also handle stationary loads well, which is why it is often used in parking spots and holding areas.
The length, width, and strength of a runway depend on the type of airport, the size of the aircraft it serves, and the volume of traffic it handles. For example, larger aircraft and higher traffic volumes require thicker pavement to support the weight and number of operations. Additionally, runway surfaces are grooved to maximize tire friction and minimize hydroplaning after heavy rains.
The construction process for a new runway can take years, from the initial planning stages to the actual paving and grooving of the surface. Regular maintenance and inspections are crucial to ensure the runway remains in good condition, as repairs can be costly and may require temporary closure of the runway.
Shuttle Service: Palm Springs Airport, AM to PM
You may want to see also
Runway length
The length of a runway is a critical factor in ensuring the safety and efficiency of aircraft operations. It directly affects an aircraft's ability to accelerate and decelerate during takeoff and landing. Runway length is determined by several factors, including aircraft type, airport elevation, weather conditions, geographical location, and other environmental considerations.
The average length of a runway at major commercial airports is usually between 8,000 and 13,000 feet. This range accommodates large commercial jets, which require longer runways to achieve the necessary speed for takeoff and landing. The length of a runway can also impact the types of aircraft that can utilize it, with larger aircraft requiring longer runways. For instance, the Boeing 747 requires nearly 12,000 feet of runway space at sea level.
The size of a runway plays a crucial role in the performance and safety of aircraft operations. Larger runways enable higher speeds and accommodate larger aircraft, which need more room to reach takeoff velocity and to slow down upon landing. A longer runway length is particularly important in hotter climates or at higher altitudes, where aircraft engines perform less efficiently. Additionally, longer runways provide a sufficient buffer for aircraft to stop safely in the event of an aborted takeoff or a rejected landing.
The elevation of an airport above sea level is another significant factor influencing runway length. Airports located at higher elevations experience decreased atmospheric pressure, resulting in reduced engine thrust due to the lower oxygen levels. Consequently, aircraft must travel at greater speeds and require longer runways to achieve a safe takeoff.
To ensure safe operations, it is essential to understand and implement the appropriate runway length for different aircraft types. During landing, a sufficient runway length is crucial to allow for a safe stopping distance after touchdown. If the runway is too short, there is a risk of overshooting the runway, posing significant safety concerns.
London Airports: Direct Flights to and from Newquay
You may want to see also
Frequently asked questions
Airport runways are made of man-made materials like asphalt, concrete, or a combination of both. The choice of pavement depends on local ground conditions, the type of aircraft using the facility, and cost.
Asphalt is a flexible surface that is more gentle on the tires during touchdown. It is also quicker and cheaper to install than concrete.
Concrete is a rigid surface that handles stationary loads well. It is also more durable and has a longer lifespan than asphalt.
Runway thickness varies from airport to airport, with commercial airports serving heavy aircraft having runway surfaces between 10 inches and 4 feet thick, including the subgrade.
The length of a runway depends on the type of airport, the size of the aircraft, and the volume of traffic. Many commercial planes, such as the Boeing 747, require nearly 12,000 feet of runway space at sea level.