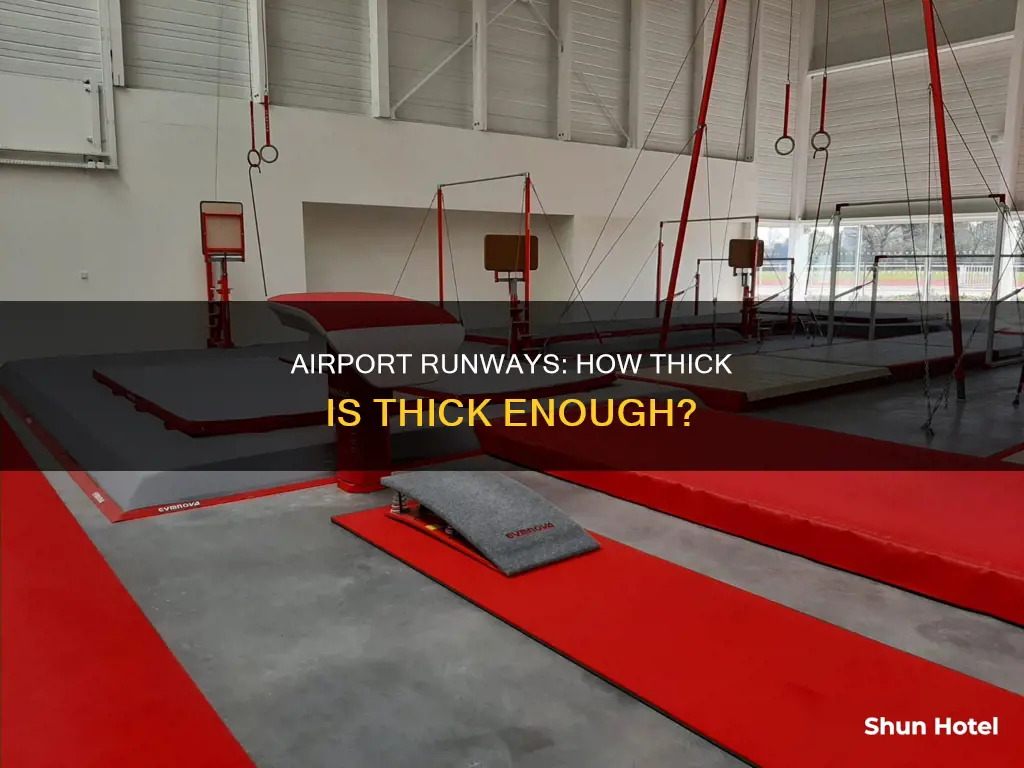
The thickness of an airport runway depends on various factors, including the type of pavement used, the weight and frequency of aircraft traffic, soil conditions, and climate. Runways are typically constructed using asphalt, concrete, or a combination of both, with each material offering unique advantages and disadvantages. Asphalt runways are flexible, cost-effective, and provide a smooth surface, but they require frequent maintenance and are sensitive to temperature changes. Concrete runways, on the other hand, are highly durable, require less maintenance, and are heat resistant, but they come with a higher initial installation cost and are prone to cracking. The thickness of rigid pavement layers in commercial service airports can range from 6 inches to 16-18 inches, while flexible pavement layers can be as thin as 3 inches.
What You'll Learn
- Runway thickness depends on usage, weight, frequency, soil, climate and material rigidity
- Rigid runways are thicker than flexible runways
- Flexible runways are more prone to damage and require more maintenance
- Concrete is more expensive and time-consuming to install than asphalt
- Composite pavements combine the strengths of asphalt and concrete
Runway thickness depends on usage, weight, frequency, soil, climate and material rigidity
The thickness of an airport runway depends on various factors, including usage, weight, frequency, soil conditions, climate, and the rigidity of the material used.
Usage and weight are crucial factors in determining runway thickness. Runways must be designed to withstand the weight of aircraft, with thicker layers required for heavier planes. Additionally, the frequency of flights impacts the thickness, as a higher number of flights will result in more wear and tear.
Soil conditions play a significant role as well. The type of soil and its ability to provide a stable foundation affect the thickness of the runway layers. Inadequate soil stability may require thicker layers to ensure a durable runway.
Climate is another important consideration. In hot climates, asphalt runways must be carefully designed to prevent softening, which could lead to surface deformation. In cold climates, asphalt can become brittle and crack, requiring additional maintenance. Concrete, on the other hand, is less susceptible to temperature variations and maintains its structural integrity in all weather conditions.
The choice between rigid and flexible pavement materials also impacts runway thickness. Rigid pavements, constructed with concrete, typically require a minimum thickness of six inches for general aviation airports. Commercial service airports often need thicker layers, ranging from 16 to 18 inches. Flexible pavements, made of asphalt, can be as thin as three inches, but the flexibility of this material allows for slight ground movements without cracking, making it suitable for variable temperatures and ground conditions.
Finally, the thickness of a runway is influenced by the desired lifespan and maintenance requirements. Reinforced concrete, for example, offers a longer service life with minimal maintenance due to its enhanced strength and resistance to cracking. However, it comes at a higher initial construction cost.
A Guide to CLT Airport's Efficient Gate System
You may want to see also
Rigid runways are thicker than flexible runways
The thickness of an airport runway depends on various factors, including pavement use, weight and frequency of traffic, soil conditions, and climate. The type of pavement, whether rigid or flexible, is a significant consideration.
Rigid runways, constructed with concrete, are thicker than flexible runways. For general aviation airports, a minimum pavement layer thickness of six inches is required for rigid pavements. However, at commercial service airports, rigid pavement layers can reach sixteen to eighteen inches in thickness. The loading factor plays a crucial role, with higher loading requiring thicker rigid pavement sections.
On the other hand, flexible pavements, constructed with asphalt, can be as thin as three inches, depending on traffic conditions. Flexible pavement sections distribute wheel loading differently, and increased loading requires thicker base and subbase course layers to effectively distribute the weight.
The choice between rigid and flexible pavements depends on the specific requirements of the airport. While rigid pavements offer durability and strength, they are more expensive and time-consuming to install. Flexible pavements, on the other hand, are more cost-effective and easier to repair but require more frequent maintenance due to their susceptibility to temperature variations.
In summary, rigid runways are thicker than flexible runways, and the thickness of both types of pavements can vary depending on factors such as loading requirements, traffic conditions, and maintenance needs.
Copenhagen Airport: Sleeping Pods for Weary Travelers?
You may want to see also
Flexible runways are more prone to damage and require more maintenance
The thickness of airport runways varies depending on several factors, including the type of pavement used, aircraft weight, traffic frequency, soil conditions, and climate. Typically, rigid pavements constructed from concrete are thicker than their flexible counterparts, which are made from asphalt.
Flexible runways, despite being more adaptable to weather conditions and easier to repair, are more susceptible to damage and require more maintenance. This is primarily due to their multi-layered structure, which includes a base layer of prepared subgrade, a granular layer, and a top layer of asphalt. While flexible pavements can withstand freeze-thaw cycles without cracking, they are more vulnerable to edge weakness and fuel sensitivity. Aircraft fuel can damage asphalt surfaces, and the edges of flexible pavements may require additional support.
In contrast, rigid pavements are constructed with a concrete slab over a granular sub-base, making them stronger and more resistant to fuel spills. They are designed to absorb the pressure of aircraft without bending, and their joints help manage thermal expansion, preventing cracks. As a result, rigid pavements last longer—up to 30 years—and require less frequent maintenance.
The choice between flexible and rigid pavements depends on various factors, including local material availability, expected aircraft traffic, and construction costs. While flexible pavements are initially cheaper, their higher maintenance needs can make them more expensive in the long run. Rigid pavements, despite their higher upfront costs, often prove more cost-effective over time due to their durability and lower maintenance requirements.
To ensure the safety and longevity of runways, engineers carefully consider these factors when selecting the pavement type. Flexible runways, despite their advantages in weather adaptability and repair ease, come with the trade-off of increased maintenance needs and a higher propensity for damage.
Traveling with Dogs: Are They Allowed at Logan Airport?
You may want to see also
Concrete is more expensive and time-consuming to install than asphalt
The thickness of airport runways varies depending on several factors, including the type of pavement, traffic weight, frequency of flights, soil conditions, and climate. Typically, rigid pavements constructed with concrete are thicker than flexible pavements made with asphalt.
Now, here are some paragraphs explaining why concrete is more expensive and time-consuming to install than asphalt:
Concrete is generally more expensive and time-consuming to install than asphalt due to several factors. Firstly, the installation process for concrete takes longer and often requires more labor, resulting in higher labor costs. Concrete also tends to have a higher upfront cost per square foot, typically ranging from $4 to $15, while asphalt is usually more affordable, ranging from $2 to $8 per square foot.
The equipment needed for laying concrete is often more specialized and costly than that required for asphalt installation. Additionally, concrete requires a longer curing time, which can impact the overall timeline of a project. Concrete can take up to seven days to completely cure before it can bear traffic, whereas asphalt typically needs only 48 to 72 hours. This longer curing time for concrete can disrupt business operations, especially for projects like parking lots or runways that require continuous access.
Another factor contributing to the higher cost of concrete is the ingredients used. Concrete is made up of aggregates, paste, and Portland cement. The careful proportioning and mixing of these ingredients contribute to its strength and durability but also increase its price. On the other hand, asphalt primarily uses aggregates, bitumen, and additives, which are generally less expensive.
It's important to note that while asphalt has a lower initial cost, it may require more frequent maintenance and repairs over time. Asphalt is more susceptible to weather conditions and heavy traffic, leading to cracks and potholes that need regular attention. Concrete, despite its higher upfront investment, offers greater durability and requires less maintenance, resulting in potential long-term cost savings.
DFW Airport's Restaurant Scene: A Comprehensive Guide
You may want to see also
Composite pavements combine the strengths of asphalt and concrete
The thickness of airport runways varies depending on factors such as the type of aircraft using the airport, the soil conditions, and the local climate.
Composite pavements, which combine the strengths of asphalt and concrete, are an excellent choice for airport runways. They offer a durable, cost-effective, and low-maintenance solution. Asphalt, also known as blacktop or pavement, is a composite material made from aggregates, bitumen, and mineral fillers. It is flexible, durable, and highly resistant to wear and deformation. On the other hand, concrete pavements are rigid structures that offer high bearing capacity and long-term durability. They are made from typical concrete materials, often with the addition of secondary cementitious materials to enhance their properties.
When combined, asphalt and concrete create a strong and resilient pavement system. The asphalt layer provides flexibility and acts as a waterproof barrier, while the concrete layer adds strength and rigidity. This combination can withstand heavy aircraft loads and is highly durable.
The thickness of composite pavements for airport runways can vary depending on the specific requirements and conditions. For general aviation airports with lower traffic, a minimum thickness of six inches for the rigid concrete layer may be sufficient. However, for commercial service airports with frequent heavy aircraft traffic, the rigid concrete layer can be as thick as sixteen to eighteen inches. The flexible asphalt layer can be as thin as three inches, but the thickness of the base and subbase courses beneath it will depend on the wheel loads and traffic frequency.
By combining the advantages of both asphalt and concrete, composite pavements provide a robust and long-lasting solution for airport runways, ensuring safe and efficient aircraft operations.
Teterboro Airport: Hotels and Accommodations Available?
You may want to see also
Frequently asked questions
The thickness of an airport runway can vary depending on various factors such as pavement use, weight and frequency of traffic, soil conditions, and climate. The thickness can range from 3 inches for flexible pavement to 16-18 inches for rigid pavement.
Rigid pavement is constructed with concrete and is commonly used in commercial service airports, while flexible pavement is made of asphalt and is used in general aviation airports.
The thickness of an airport runway depends on several factors, including the type of aircraft using the runway, the frequency of flights, and the weight of the aircraft.
Asphalt is a flexible material that can accommodate slight ground movements without cracking, making it suitable for areas with variable temperatures and ground conditions. It also provides a smooth surface, reducing wear and tear on aircraft tires and landing gear.
Concrete is extremely durable and can withstand heavy loads and high traffic. It requires less frequent maintenance compared to asphalt and is more heat resistant.