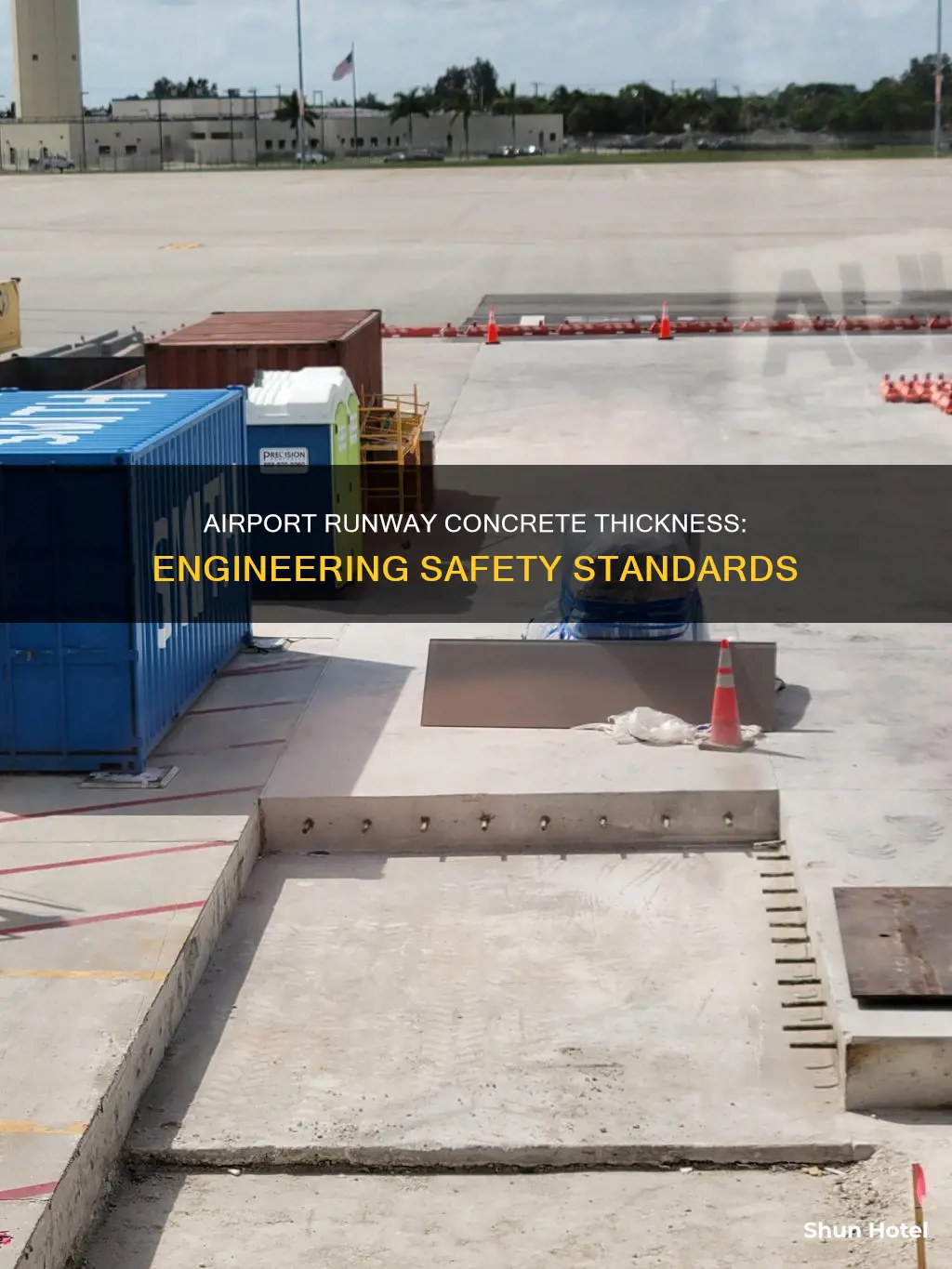
Airport runways are constructed from materials that offer exceptional durability, strength, and resistance to various environmental conditions. The thickness of airport runway concrete depends on several factors, including the type of airport, the size of aircraft it serves, and the volume of air traffic. Typically, runway surfaces range in thickness from 10 inches to 4 feet, including the subgrade. The choice between asphalt and concrete depends on local ground conditions, aircraft types, and cost considerations. Concrete runways, though more expensive, offer enhanced durability and longevity. The concrete at George Bush Intercontinental Airport in Houston, Texas, for example, is predicted to last about 120 years.
What You'll Learn
Concrete vs asphalt runways
The choice between concrete and asphalt runways depends on various factors, including upfront cost, maintenance, durability, and environmental considerations. While both materials offer distinct advantages, the decision is based on specific airport requirements, such as climate, traffic, and raw material availability. Here is a detailed comparison between concrete and asphalt runways:
Initial Cost and Installation:
Concrete runways incur higher upfront costs and require more time for installation compared to asphalt. The process involves formwork and curing time, contributing to increased labor hours and material expenses. In contrast, asphalt runways offer a more cost-effective initial installation, making them a financially attractive option.
Maintenance and Repair:
Asphalt runways are easier and quicker to repair than concrete. Minor damages, such as potholes, can be patched efficiently, minimising runway downtime. However, asphalt requires more frequent maintenance and resurfacing due to wear and degradation over time. Concrete runways, on the other hand, boast superior durability and require less frequent maintenance, reducing long-term maintenance costs.
Durability and Environmental Factors:
Concrete runways excel in durability, withstanding heavy loads and high traffic. They are ideal for large airports with frequent operations of large aircraft. Additionally, concrete is less susceptible to temperature variations and maintains its structural integrity in hot conditions, unlike asphalt, which can soften and deform in extreme heat. This makes concrete a more environmentally friendly option, as asphalt uses a petroleum-based binder.
Flexibility and Smoothness:
Asphalt runways offer flexibility, accommodating slight ground movements without cracking. This adaptability makes them suitable for regions with variable temperatures and ground conditions. Asphalt also provides a smooth surface, reducing wear and tear on aircraft tires and landing gear. Concrete runways, while strong, are more prone to cracking, especially in freeze-thaw conditions, and repairing these cracks can be challenging and costly.
Composite Pavements:
In some cases, airports utilise composite pavements that combine asphalt and concrete layers. These runways have a concrete base overlaid with an asphalt surface, offering a balance between flexibility and durability. Composite pavements can be customised to meet specific performance requirements, such as enhanced load-bearing capacity or improved smoothness. However, they come with higher initial construction costs and require specialised installation techniques.
Airport Wi-Fi: WPS and AOSS Support for Travelers
You may want to see also
Composite pavements
The second layer, positioned above the subgrade, is the graded granite aggregate base. This layer includes a specific mix of coarse to medium-grained materials such as sand, gravel, and crushed stone. These materials are combined in precise proportions to enhance the foundation's stability and drainage capabilities.
The third layer is the cement-treated base (CTB), which combines granular soil, aggregates, cement, and water. This combination forms a stabilized layer that adds significant strength and durability to the runway structure.
The fourth and topmost layer is the hot mix asphalt concrete, which constitutes the runway's surface. This layer consists of asphalt mixed with aggregates, providing a smooth, durable, and flexible surface for aircraft operations. The asphalt layer is crucial for handling thermal expansion and contraction and offering good friction for landing and takeoff.
Airports in South Carolina: A Comprehensive Guide
You may want to see also
Subbase and base layers
The subbase and base layers of an airport runway are crucial components that provide a stable foundation for the entire structure. These layers are typically made of crushed stone, gravel, or other aggregates, meticulously compressed layer by layer to ensure stability and distribute weight evenly.
The subbase layer is the unsung hero of runway construction, serving as the thickest layer and providing a sturdy foundation. It is composed of native soil, meticulously compacted to create a solid base that can withstand the immense weight of aircraft and the frequent usage of busy airports.
Positioned above the subbase is the base layer, or graded granite aggregate base. This layer is a carefully crafted mix of coarse to medium-grained materials, including sand, gravel, and crushed stone. The specific proportions of these materials are combined to enhance the overall stability and drainage capabilities of the runway.
The base layer also includes a cement-treated base (CTB), which adds significant strength and durability. This CTB layer combines granular soil, aggregates, cement, and water to form a stabilised foundation.
Together, the subbase and base layers work in harmony to enhance the runway's load-bearing capacity, improve drainage, and prevent the surface layer from settling and deforming over time. Their preparation and compaction are crucial steps in ensuring the stability and longevity of the runway.
By utilising these carefully selected materials and following precise construction techniques, engineers can create a runway foundation that is strong, durable, and capable of supporting the demanding requirements of modern aviation.
Bend, Oregon: Airport Accessibility and Ease of Travel
You may want to see also
Runway rubber removal
The accumulation of rubber deposits on runways is a common issue for airports, particularly in the touchdown zone where the landing gear wheels start rotating, causing friction that peels rubber off the tyres. These rubber deposits can have several adverse effects, including:
- Obliterating runway markings, potentially confusing pilots.
- Becoming slippery when wet, contributing to runway excursions.
- Reducing friction, which is necessary for aircraft to stop during landing.
- Causing uneven build-up, which can become a hazard for aircraft engines.
To address these issues, several methods for removing rubber deposits from runways have been developed:
Chemical Solvents
This method involves spraying a solvent solution onto the contaminated area, waiting for a specified time, and then washing and sweeping the area. Different chemical agents are used depending on the surface type (e.g., concrete or asphalt). This approach requires caution due to the aggressive nature of the cleaning compounds, which can damage paint and pavement surfaces if not properly controlled.
High-Pressure Water Blasting
This mechanical method uses ultra-high-pressure water pumps (up to 40,000 PSI) with a low flow rate to remove rubber deposits without damaging the runway surface. The equipment ranges from manually operated nozzles to self-propelled semi-trailers with high-pressure water spray bars. While effective for lightly contaminated areas, its effectiveness decreases with deeper contamination.
Combination of Chemical Solvents and High-Pressure Water Blasting
This modern approach involves first dissolving rubber deposits with chemical solvents and then thoroughly flushing the area with high-pressure water blasting.
Hot Compressed Air
This technique uses high-temperature gases (approximately 1200°C) emitted at high speed to burn away rubber deposits. While it is claimed to have a low risk of loosening the surfacing material, caution is still advised, especially when used on asphaltic concrete runways. A small amount of carbon deposit is produced on concrete surfaces, which can be brushed off using a tractor- or truck-mounted brush machine.
Specialised equipment, such as the Stripe Hog, has been developed to efficiently perform runway rubber removal using these methods. The Stripe Hog, for example, can remove rubber from asphalt and concrete runways at rates of 40,000 sq. ft/hr (3,716 m2/hr) and is known for its versatility, efficiency, and quick removal of airport markings and rubber without causing significant damage to the surface.
The Best Airport Options for Panama City Beach
You may want to see also
Runway thickness calculations
The thickness of an airport runway is a critical factor in ensuring the safety and functionality of aircraft operations. The calculation of runway thickness involves various factors, including load-bearing capacity, aircraft weight, and traffic volume. Here are the key considerations and steps involved in determining the appropriate thickness for a runway:
Load-Bearing Capacity
The runway must be designed to withstand the weight of aircraft, which varies depending on the type of aircraft and their load. The load-bearing capacity of the runway is influenced by the materials used, such as concrete, asphalt, or a combination of both. Concrete runways are known for their high durability and strength, requiring less frequent maintenance compared to asphalt. On the other hand, asphalt runways offer flexibility and are less susceptible to cracking in cold climates.
Aircraft Weight
The weight of the aircraft using the runway is a significant factor in determining the required thickness. Larger aircraft, such as wide-body jets, require thicker runways to distribute the weight and ensure a stable surface. The maximum weight an aircraft can reach must be considered when calculating the thickness of the runway.
Traffic Volume
Airports with a high volume of aircraft traffic will require thicker runways to withstand the frequent usage. The number of takeoffs and landings, as well as the frequency of heavy aircraft operations, will impact the thickness calculations. Busier airports with frequent heavy aircraft movements may opt for concrete runways due to their longevity and minimal maintenance requirements.
Environmental Conditions
The local environmental conditions, including temperature variations and ground stability, play a role in determining runway thickness. In areas with extreme temperatures, the choice of material and thickness can help prevent softening or cracking of the runway surface. Additionally, unstable ground conditions may require a thicker runway to ensure stability and prevent settling over time.
Runway Design and Construction
The design and construction of the runway involve multiple layers, each serving a specific purpose. A typical runway consists of a subgrade layer, a base layer, a treated base layer, and a surface layer. The thickness of each layer is calculated based on the expected loads, drainage requirements, and the overall strength needed to support aircraft operations.
Safety Considerations
In summary, the calculation of runway thickness involves a comprehensive analysis of various factors, including load-bearing capacity, aircraft weight, traffic volume, environmental conditions, and safety considerations. By carefully considering these factors, engineers can design and construct runways that meet the specific demands of modern aviation while ensuring the safety and efficiency of aircraft operations.
Galaxy 7: Airport Ban and Its Impact
You may want to see also
Frequently asked questions
Airport runway concrete thickness varies. Commercial airports serving heavy aircraft have runway surfaces with a thickness between 10 inches and 4 feet, including the subgrade.
The thickness of the runway surface depends on the type of airport, the size of aircraft most commonly served, the volume of traffic, and the condition of the soil that forms the subbase.
Airport runways are constructed using man-made materials such as asphalt, concrete, or a combination of both.
Concrete is extremely durable and can last several decades with minimal maintenance. It is ideal for large airports with frequent and heavy aircraft operations. Concrete runways also require less frequent maintenance than asphalt runways, reducing long-term maintenance costs.
Concrete runways have a higher initial installation cost and take longer to install compared to asphalt. Concrete is also prone to cracking, especially in freeze-thaw conditions, and repairing concrete cracks can be challenging and expensive.