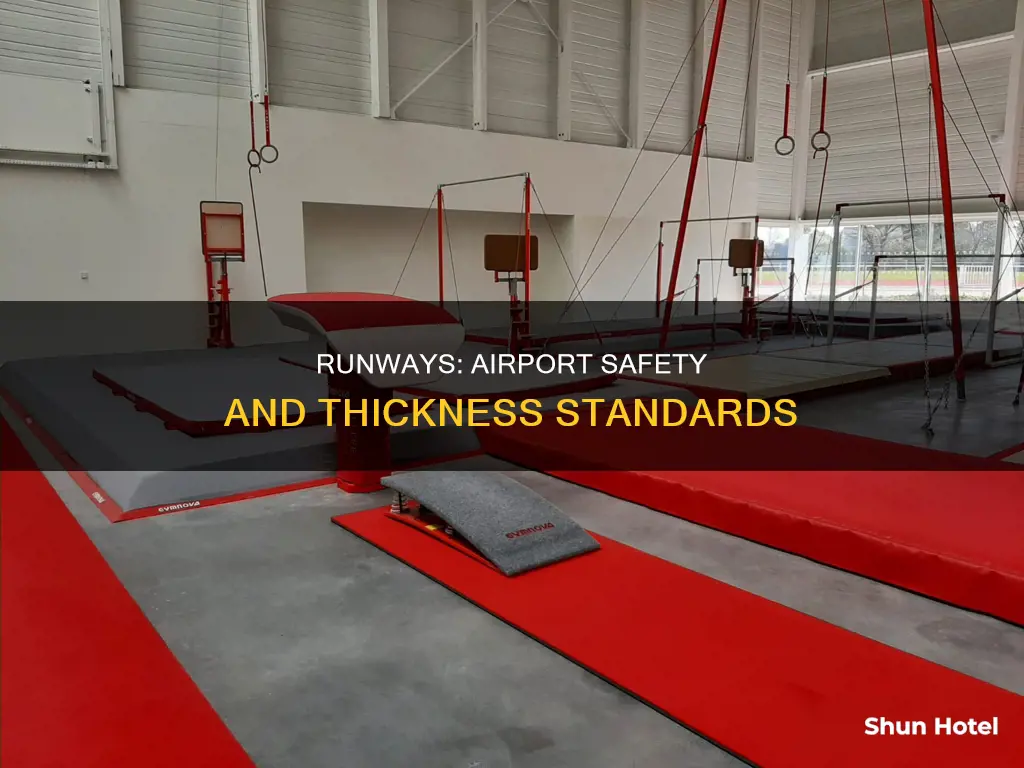
The thickness of airport runways varies depending on the materials used, the weight of the aircraft, and the local ground conditions. Typically, a runway is more than 2.5 meters thick and consists of four distinct layers: the subgrade, graded granite aggregate base, cement-treated base, and the topmost layer, which is usually asphalt or concrete. The subgrade layer, composed of native soil, is the thickest and can be up to 10 feet deep. The thickness of the entire runway, including the subgrade, can range from 10 to 48 inches (25 to 122 cm) for heavy-duty commercial aircraft.
What You'll Learn
Asphalt vs. concrete
The majority of runways are either asphalt or concrete surfaces. While asphalt is more common, both have their own advantages and disadvantages.
Composition
Asphalt and concrete are formed from aggregates—a set of rocks available in coarse (larger) and fine (smaller) sizes. Aggregates make up 60-75% of a concrete mix, with the remainder being a paste consisting of water (14-21%) and cement (7-15%). Concrete also contains 8% air, which gives it some workability when freshly mixed. Asphalt, on the other hand, contains a different binding agent—a petroleum-based hydrocarbon mixture, which gives it a darker brown or black appearance.
Installation and Repair
Concrete is more expensive and time-consuming to install and repair than asphalt. It is generally stronger, but more prone to cracking, which increases the frequency and cost of repairs. Asphalt, on the other hand, is faster to repair.
Climate and Conditions
Concrete is more environmentally friendly due to asphalt's petroleum-based binder. It is also more suitable for hot conditions as asphalt can deform under high temperatures. Concrete, however, is notorious for cracking when exposed to extreme temperatures.
Load and Traffic
Concrete handles stationary loads well, whereas asphalt can deform on warm days. Concrete reinforcements are often found under asphalt runways, especially in areas subject to more pressure, such as the ends of runways where large and heavy aircraft land.
Overall
Both asphalt and concrete are legitimate surfaces for runways, and the choice between the two depends on various factors including climate, traffic, and raw material access. Concrete may be preferred for its strength and environmental benefits, while asphalt is a more flexible and faster option.
Airports and ID Checks: When and Where to Expect Them
You may want to see also
Runway thickness varies
A standard runway is composed of multiple layers, each serving a specific function and contributing to the overall thickness. The base layer, known as the subgrade, is made of compressed native soil and is the thickest part of the runway. Above this is the graded granite aggregate base layer, which includes a mix of coarse and medium-grained materials for enhanced stability and drainage. The third layer, known as the cement-treated base, combines granular soil, aggregates, cement, and water for added strength and durability. The topmost layer is typically made of hot mix asphalt concrete, providing a smooth and flexible surface for aircraft operations.
The thickness of the entire runway, including the subgrade, can range from 10 to 48 inches (25 to 122 cm) for heavy-duty commercial aircraft. This thickness takes into account the different layers and their respective contributions to the overall strength and durability of the runway.
The choice of materials for the top layers can vary. Asphalt runways are more flexible and suitable for variable temperatures, but they require more frequent maintenance and are sensitive to extreme heat and cold. Concrete runways, on the other hand, are extremely durable and require less frequent maintenance but are more expensive and time-consuming to install. Reinforced concrete, which incorporates steel bars or mesh, further increases the strength and load-bearing capacity of the runway but comes at a higher cost and construction complexity.
Additionally, the thickness of a runway can be influenced by the size and weight of the aircraft it is designed to accommodate. Larger aircraft, including wide-body jets, require longer and stronger runways to facilitate safe takeoff and landing. The Boeing 747, for example, is known for having a long takeoff distance, influencing the design of runways at major international airports.
In summary, runway thickness is not uniform and depends on various factors, including aircraft specifications, ground conditions, and the choice of construction materials. Each layer of the runway serves a specific purpose, contributing to the overall thickness, strength, and functionality of the runway.
Domestic Air Travel: Exploring America's Vast Airport Network
You may want to see also
Reinforced concrete
The thickness of reinforced concrete runways can vary depending on the specific requirements and conditions of the airport. In general, concrete runways tend to be thicker near the touchdown zones and thinner towards the middle, where aircraft have usually completed their landing and are rolling towards the taxiway. For example, at Austin-Bergstrom Airport, the new concrete runway (17L-35R) is 16 inches thick, while the rehabilitated concrete runway (17R-35L) is 23 inches thick.
The construction of reinforced concrete runways involves multiple layers, each serving a specific purpose. Below the concrete surface, there is typically a base layer of clay, followed by a layer of cement sand, and then the reinforced concrete layer with embedded corrosion-coated steel bars. Additionally, electrical conduit and lighting fixtures are integrated into the rebar matrix to accommodate runway lighting and signage systems.
The benefits of using reinforced concrete for airport runways include its durability, long lifespan, and resistance to damage. It can withstand heavy aircraft loads and frequent usage, making it a suitable choice for large airports with frequent and heavy aircraft operations. However, the installation process is more complex and costly compared to other materials due to the need for skilled labour and careful construction practices.
Overall, reinforced concrete is a preferred option for major airport runways due to its enhanced structural integrity and ability to handle the demands of modern air travel. The thickness and composition of the concrete can be customised to meet specific airport requirements, ensuring safe and efficient aircraft operations.
Miami Airport's Sleeping Pods: A Traveler's Comfort
You may want to see also
Composite pavements
The thickness of a runway is generally more than 2.5 meters, and composite pavements are constructed with four distinct layers. The first layer, the subgrade, is the base layer and the thickest of all. It is composed of native soil that is meticulously compressed layer by layer to create a stable foundation. The second layer, the graded granite aggregate base, includes a mix of coarse to medium-grained materials such as sand, gravel, and crushed stone. These materials are combined in precise proportions to enhance the foundation's stability and drainage capabilities.
The third layer, the cement-treated base (CTB), combines granular soil, aggregates, cement, and water to form a stabilized layer that adds strength and durability to the runway structure. The topmost layer is the hot mix asphalt concrete, which provides a smooth, flexible, and durable surface for aircraft operations. This layer is crucial for handling thermal expansion and contraction and offering good friction for landing and takeoff activities.
Exploring Naples Airport: The Number of Gates and More
You may want to see also
Runway maintenance
Common Runway Maintenance Tasks
- Debris Removal: Keeping the runway clear of debris is essential to prevent foreign object damage to aircraft and ensure a smooth surface. Regular inspections are conducted to identify and remove any debris, including rubber deposits caused by tire friction during landings and takeoffs.
- Crack Sealing and Repaving: Cracks in the runway surface can compromise its structural integrity and must be sealed or repaired promptly. Repaving may be necessary for more extensive damage, requiring the closure of the runway and the use of heavy machinery, such as tipper trucks, excavators, and bulldozers.
- Drainage and Water Runoff: Proper drainage systems are crucial to prevent water accumulation on the runway, which can affect friction and cause aquaplaning. Grooves are cut into the runway surface to facilitate rainwater runoff, and some asphalt surfaces employ a porous top layer to allow water to drain below the surface.
- Snow and Ice Removal: During winter, snow and ice removal are essential to maintain runway operations. Airports use specialized equipment, such as snow plows, blowers, and dump trucks, and apply chemicals to prevent ice buildup.
- Lighting and Markings: Maintaining adequate lighting and visible markings on the runway is vital for safe aircraft navigation. Runway lights must be regularly inspected and maintained, and the runway surface is repainted with special solvent-based acrylic line paint as part of repaving work.
- Friction Testing: Runway friction testing is conducted to assess the braking performance and overall safety of the runway. Friction testers measure the friction coefficient between the runway and aircraft tires, helping to identify areas requiring maintenance and ensure optimal braking performance.
- Emergency Response: Airports have comprehensive emergency response plans to handle various scenarios, including aircraft accidents or malfunctions. Runway safety during emergencies involves clearing the runway of any debris, fuel spills, or other hazards, and airport personnel are trained to respond quickly and efficiently.
Timing of Runway Maintenance
To minimize disruptions, runway maintenance is typically performed at night when the airport is closed or has alternative runways available. This provides an uninterrupted window for maintenance crews to work efficiently. When a runway is scheduled for maintenance, airports issue a Notice to Airmen/Notice (NOTAM) to advise airlines and pilots of the closure.
Impact of Weather on Runway Maintenance
Weather conditions significantly impact runway maintenance and safety. Airports must monitor weather forecasts and implement measures to mitigate the effects of rain, snow, ice, and extreme temperatures. De-icing and anti-icing procedures, for example, are crucial during winter months to maintain safe runway operations.
Can Dogs Fly? Tucson Airport Pet Policy Explained
You may want to see also