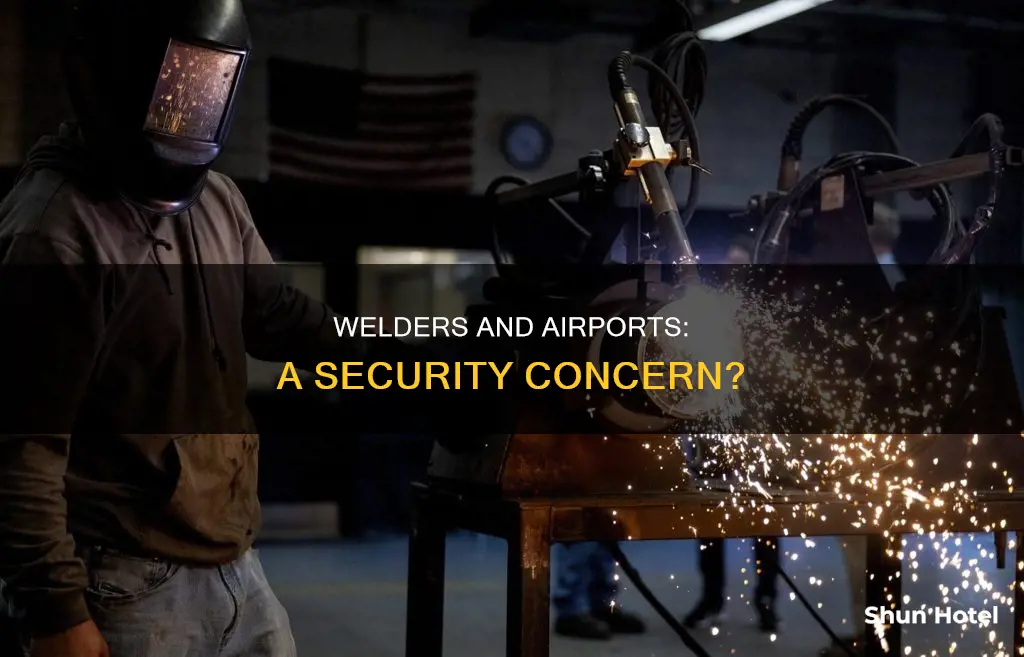
Welders are employed in a variety of industries, including aerospace, agriculture, automotive, construction, infrastructure, manufacturing, military, railroads, and shipbuilding. Welding is used in the construction and repair of aircraft, and airports all over the world employ welders. However, it is unclear if welders themselves have trouble at airports.
What You'll Learn
- Do welders need additional certifications to work at airports?
- What are the health and safety risks for welders working at airports?
- What are the key skills needed for welders working at airports?
- What are the average salaries for welders working at airports?
- What are some companies that hire welders to work at airports?
Do welders need additional certifications to work at airports?
Welding is a highly versatile process used in various industries, including aerospace. Aerospace welding is a specific niche within the welding industry, and it involves using welds to join metallic components and provide structural support in the construction of aircraft and spacecraft.
Due to the critical nature of aerospace welding, additional certifications and qualifications are required for welders working in this industry. Here are the key requirements for welders seeking to work at airports or in the aerospace industry:
Education and Training
To become an aerospace welder, a high school diploma or GED is typically the minimum requirement. However, many employers prefer candidates with an associate's degree or a four-year degree in welding technology, welding and fabrication, or a related field. These academic programs provide a strong foundation in welding techniques, materials science, and industry-specific applications.
Certifications and Examinations
In addition to academic qualifications, welders seeking to work in aerospace manufacturing need to obtain specific certifications. The American Welding Society (AWS) administers an exam that consists of a written component and a hands-on welding test. Passing this exam is crucial for demonstrating competency and obtaining the necessary certification to work in the aerospace industry.
Hands-On Experience
While education and certifications are essential, hands-on experience is highly valued in the aerospace industry. Aspiring aerospace welders can gain practical experience through internships, apprenticeships, or working in related fields. Internships within welding shops or training schools can provide valuable on-the-job training. Alternatively, finding a job as an apprentice allows you to gain free training while working for someone else.
Skill Set
Aerospace welders need a unique set of skills to excel in their field. They must be proficient in reading and understanding welding symbols, blueprints, and drawings. Accuracy, attention to detail, and the ability to follow instructions are crucial. Additionally, aerospace welders should possess a strong understanding of safety protocols and work habits, as well as knowledge of various welding techniques, such as gas welding, arc welding, and oxyacetylene gas welding.
Job Application and Requirements
When applying for an aerospace welding job, be prepared for a comprehensive process that may take a month or more. Employers will typically request a resume detailing your work experience, education, skills, and references. You may also undergo a background check and a drug test as part of the screening process. Additionally, you will likely be required to demonstrate your welding skills through a welding test.
In conclusion, welders seeking to work at airports or in the aerospace industry need to obtain specific certifications, education, and hands-on experience. The requirements outlined above ensure that aerospace welders possess the necessary skills, knowledge, and qualifications to work on critical aerospace structures, such as aircraft and spacecraft. By meeting these standards, welders can find rewarding career opportunities in this exciting and challenging field.
US Airports: Duty-Free Shopping and You
You may want to see also
What are the health and safety risks for welders working at airports?
Welding is a fabrication process that involves fusing two or more parts using heat, pressure, or both. It is commonly used in various industries, including aerospace. Welders working at airports typically work indoors, in hot and noisy conditions, and face several health and safety risks.
One of the most severe risks welders face is electric shock, which can be fatal. Electric shocks can occur when a welder comes into contact with two metal objects with a voltage between them. There are two types of electric shocks: primary voltage shock and secondary voltage shock. Primary voltage shock occurs when a welder touches an energised welding or electrode circuit with a high voltage, while secondary voltage shock happens when a welder touches the welding or electrode circuit with one hand and a grounded metal object with the other. To mitigate this risk, welding machines and workpieces should be properly grounded, and safety equipment such as insulated electrode holders should be used.
Welding also produces harmful fumes and gases that can lead to health issues. These fumes and gases depend on the type of welding and materials used and can include argon, helium, carbon dioxide, and nitrogen. The fumes may contain harmful metals such as aluminium, beryllium, lead, and manganese. Prolonged exposure to these fumes and gases can cause short-term effects like dizziness, nausea, and irritation to the eyes, nose, and throat, as well as long-term problems like lung damage, cancer, and neurological issues. Ventilation and fume extraction systems are crucial to controlling welding fumes, and respiratory protection may also be necessary.
Additionally, welding generates heat, sparks, and hot spatter, which pose fire and explosion risks, especially when performed near storage areas for flammable substances or in environments with flammable vapours or gases. "Hidden fires" can also occur when sparks or hot metal ignites materials inside walls or under flooring after welding has been completed. To prevent fires, all flammable and combustible materials should be removed from the welding area, and a fire watch should be posted during and after welding operations.
Welders are also at risk of radiation exposure from the bright visible light, ultraviolet (UV), and infrared (IR) radiation produced by welding arcs. UV radiation can cause "welder's flash" or "arc eye," while long-term exposure can lead to cataracts. IR radiation can cause burns to the skin and eyes, and intense visible light can damage the retina. Regular breaks and the use of welding curtains or screens can help reduce radiation exposure, and eye protection is essential to prevent eye damage.
Furthermore, the nature of welding work can lead to physical injuries, including musculoskeletal disorders (MSDs), repetitive strain injuries (RSIs), and soft tissue injuries to the wrists, arms, shoulders, legs, or neck. Poor housekeeping in welding workspaces can create additional hazards, with cluttered areas leading to tripping and falling risks. Welders should also be aware of the risks of fatigue and dehydration, which can impact their health and safety. Structured rest breaks and proper hydration are important to mitigate these risks.
Overall, welders working at airports face several health and safety risks, including electric shock, exposure to harmful fumes and gases, fire hazards, radiation exposure, physical injuries, and the risks associated with a cluttered or poorly maintained workspace. It is crucial to follow safety protocols and use appropriate personal protective equipment (PPE) to mitigate these risks.
Mumbai Airport Quarantine: What's the Protocol?
You may want to see also
What are the key skills needed for welders working at airports?
Welders are in high demand across a variety of industries, including aerospace, automotive, and construction. Working at an airport as an aerospace welder requires a specific skill set and qualifications beyond what is taught in trade school. Here are the key skills needed for welders working in this niche field:
Technical Knowledge and Skills
Aerospace welding involves joining metallic components and structures used in aircraft and spacecraft construction. Aerospace welders need to have a comprehensive understanding of different metals, their properties, and how they react to various welding techniques. They must know how to weld different metals such as aluminum, steel, and titanium. Additionally, they should be familiar with various welding processes, including Gas Tungsten Arc Welding and Metal Inert Gas (MIG) or Tungsten Inert Gas (TIG) welding techniques. Understanding blueprints and technical drawings is also crucial to pinpointing the exact weld requirements and ensuring stable constructions.
Attention to Detail
Aerospace welding demands extreme precision and accuracy. Even a slight error can have disastrous consequences for an aircraft or spacecraft. Welders must be meticulous in their work, checking and double-checking their results to ensure compliance with safety standards and prevent structural problems.
Manual Dexterity
Welding is a physically demanding job that requires good hand-eye coordination and steady handwork. Aerospace welders need to hold and manipulate heavy equipment and work with challenging materials in hot and noisy conditions. Having a strong grip and the ability to hold torches in a steady position for extended periods are essential skills.
Strength and Endurance
Working as an aerospace welder can be physically strenuous, requiring strength and endurance to handle heavy gear and materials. Core and upper body strength are particularly important, and welders should be able to hold, move, and manipulate the equipment with ease. Regular strength training and cardio exercises can help improve physical stamina for this demanding role.
Spatial Orientation
Aerospace welders often need to work on complementary parts or joints, which requires them to understand and manipulate objects in their environment from different angles and orientations. The ability to visualize and work with objects in three-dimensional space is crucial to ensuring the final product is oriented correctly and meets specifications.
Safety Awareness
Aerospace welding involves working with hazardous materials and equipment, including flammable gases, intense heat, and heavy objects. Welders must be well-versed in industrial safety practices and know how to use protective equipment, such as goggles, gloves, face shields, and respirators, to safeguard themselves and their colleagues.
Education and Certifications
To become an aerospace welder, individuals typically need a high school diploma or GED, followed by an associate's or four-year degree in welding technology, welding and fabrication, or mechanical engineering. Obtaining certifications from organizations like the American Welding Society (AWS) is also essential for working in aerospace manufacturing. Staying up-to-date with industry trends, such as robotic welding and laser beam welding, is crucial for continuous development in this field.
Airport Security: Do They Search Checked Bags?
You may want to see also
What are the average salaries for welders working at airports?
Welders working in the aerospace industry, also known as aerospace welders, are in high demand. They are responsible for welding in aircraft and spacecraft, and often work in airports or aircraft factories. The work is both physically and mentally demanding, requiring a strong focus on safety.
The salary of an aerospace welder can vary depending on several factors, including experience, company, and location. On average, aerospace welders earn between $20 and $30 per hour, which amounts to about $851 per week, $3,688 per month, and $44,260 per year. However, wages can be higher for welders working on larger aircraft projects. Additionally, aerospace companies tend to pay their welders more than oil and gas companies.
Aerospace welders' salaries can also be influenced by the benefits offered by their employers. For example, some companies provide health insurance and retirement plans, which contribute to a higher total compensation package.
Experience plays a crucial role in determining the salary of an aerospace welder. The more years of experience a welder has, the higher their earning potential. For instance, welders with over ten years of experience can expect to earn an average of $52,205 per year.
When it comes to location, the salary of aerospace welders can vary significantly across the United States. For example, in 2024, the average annual salary for a welder in California was $50,101, while in Texas, it was $44,689.
To summarise, welders working at airports or in the aerospace industry can expect to earn competitive salaries, especially if they possess extensive experience and expertise. The specific wages will depend on factors such as project complexity, company, benefits, and location.
Airports and Drug Testing: What's the Protocol?
You may want to see also
What are some companies that hire welders to work at airports?
Welders are a crucial component of the aerospace industry, and as such, there are many companies that hire welders to work at airports.
One such company is Airport Welding & Muffler, a family-owned and operated business located on Harvey Air Field in Snohomish, Washington. Airport Welding & Muffler has been in operation since 1972 and primarily services cars, trucks, and motor homes. They offer a range of services, including muffler repair, custom pipe bending, and trailer hitch installation.
Another company that hires welders to work at airports is the aerospace manufacturing industry. Aerospace welders are responsible for the manufacture and repair of airplanes, jets, and helicopters. To become an aerospace welder, one must typically obtain a four-year degree in welding and fabrication, pass a certification exam, and gain hands-on experience through internships or apprenticeships.
Additionally, some welding companies may be contracted to work on airport construction projects. Welders are essential to the success of any construction project, creating the metal framework for buildings and bridges and working on cutting and repairing beams, columns, and girders.
Overall, while I cannot provide an exhaustive list, there are certainly several companies that hire welders to work at airports, including airport-based businesses, aerospace manufacturers, and construction contractors.
Airports and COVID Testing: What's the Protocol?
You may want to see also
Frequently asked questions
Welders are essential to the construction and repair of aircraft, so they are commonly found working at airports.
Aerospace welding is used to join metallic components and structures and to provide structural support. It differs from other welding processes as the welds are scrutinized for cleanliness and are heated to high temperatures and cooled quickly.
Aerospace welders use a variety of materials, including steel alloys, inconel, chromoly, high-alloy tool steel, superalloys, and aluminum nickel arc rods.
To become an aerospace welder, you typically need a high school diploma or GED, followed by an associate's degree in welding technology or a related field. You will also need to pass a certification exam administered by the American Welding Society (AWS).
Aerospace welders are responsible for the manufacture and repair of aircraft, including airplanes, jets, and helicopters. They work with a variety of materials and techniques to produce high-quality welds, ensuring the structural integrity and safety of the aircraft.